From Design to Mass Production: How One-Stop PCB Customization Speeds Up Your Development Cycle
- SUNSOAR TE.
- 2 days ago
- 2 min read
Bringing an electronic product from concept to market is a race against time. You’ve got the idea. The design is in place. But as you move into prototyping, sourcing components, and finally mass production, the delays start stacking up. That’s where one-stop PCB customization services come in — and why they’ve become a game-changer for startups and hardware developers alike.
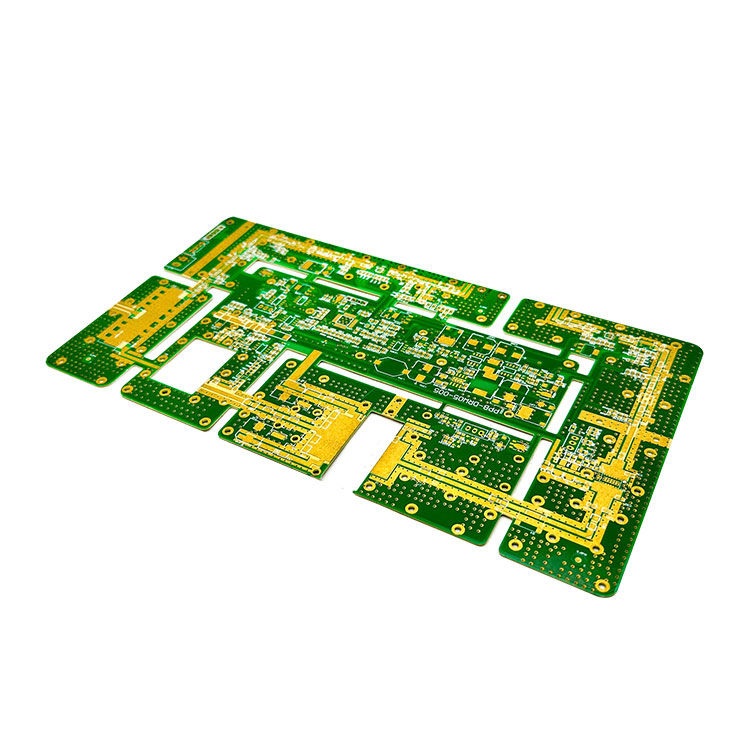
The Problem: Fragmented Supply Chains Kill Time
In traditional PCB development, each stage involves a different partner. You design the board with one provider, prototype it elsewhere, buy components from another vendor, and finally find a factory to handle PCBA and assembly. While this approach may give you flexibility, it comes with a heavy price: coordination complexity, communication gaps, and unexpected delays.
Every handoff in this fragmented process increases the risk of:
Inconsistent quality
BOM errors
Sourcing mismatches
Missed deadlines
Hidden costs
In today’s fast-paced electronics market, these delays can cost you customers and competitive advantage.
The Solution: One-Stop PCB Customization
One-stop PCB customization integrates the entire product development cycle under a single roof — from layout and prototyping to components sourcing, SMT assembly, functional testing, and packaging.
Here’s how this model accelerates your development:
1. Faster Turnaround Time
With in-house teams collaborating in real time, your prototype can be manufactured, assembled, and tested in days — not weeks. Communication gaps are minimized, and issues get solved faster.
2. Smoother Design Iterations
Need a quick tweak after your first round of testing? With one provider handling everything, modifications can be implemented immediately without the back-and-forth between separate vendors.
3. Lower Costs
By consolidating production, you reduce shipping expenses, procurement markups, and administrative overhead. Some manufacturers — like us at Sunsoar — even offer free DFM checks to spot cost-saving design improvements upfront.
4. Higher Quality Assurance
One team is accountable for your project end-to-end. This reduces the chances of finger-pointing when problems occur. Plus, consistent QC standards ensure better reliability.
5. Streamlined Procurement
Sourcing components? A one-stop partner with global procurement experience can help you avoid shortages, spot counterfeit risks, and suggest cost-effective replacements — especially helpful in volatile markets.
Who Benefits the Most?
One-stop PCB services are ideal for:
Startups needing fast prototyping and quick pivots
Engineers managing complex or multilayer designs
Hardware companies scaling to small or medium batch production
OEMs seeking reliability with minimal management overhead
Whether you're developing consumer electronics, medical devices, automotive systems, or IoT gadgets — the efficiency and agility of a one-stop model can shorten your time-to-market dramatically.
Final Thought: Speed Isn’t Everything — But It Matters
In the world of electronics, the ability to iterate quickly, adapt rapidly, and launch confidently can be your biggest competitive edge. A one-stop PCB partner helps you stay focused on innovation, not chasing down suppliers or fixing avoidable mistakes.
If your team is ready to cut development time by 30-50% — while improving quality and cost control — let’s talk. We’ve helped 1000+ customers do just that.
Comentarios