The Impact of PCB Material Choices on Performance and Cost
- SUNSOAR TE.
- Jun 7
- 3 min read
Printed Circuit Boards (PCBs) serve as the foundation for nearly every electronic device. Yet, beyond the complexity of layout design and assembly processes, one factor plays a pivotal role in both performance and cost: the material choice. The base material used in a PCB directly affects signal transmission, thermal stability, durability, and ultimately, how the end product functions in real-world conditions.
In a competitive marketplace where both performance and budget are critical, understanding how different PCB materials influence the final product is essential.
Understanding the Layers: What Makes Up a PCB?
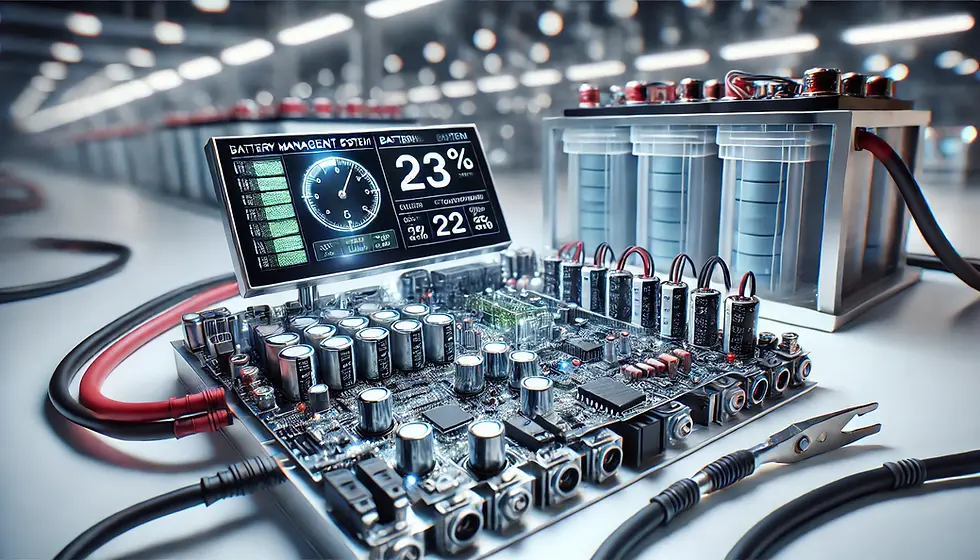
At its core, a PCB is composed of several layers:
Substrate/Base Material: Usually fiberglass-reinforced epoxy laminate (FR4), ceramic, or polyimide.
Copper Layer: Provides the conductive pathways.
Solder Mask: Insulates and protects the copper.
Silkscreen: Used for labeling and identification.
While the copper and solder mask receive a lot of attention during design, the base material is what determines mechanical strength, dielectric constant, thermal performance, and signal integrity.
Common PCB Materials and Their Characteristics
1. FR4 (Flame Retardant 4)
The industry standard for most general-purpose electronics, FR4 is made from woven glass fiber and epoxy resin.
Pros: Low cost, decent mechanical strength, good insulation.
Cons: Limited thermal performance, not ideal for high-frequency applications.
2. High-Frequency Laminates (e.g., Rogers, Teflon)
Used in applications such as RF communication, satellites, and radar systems.
Pros: Stable dielectric constant, low signal loss, high-frequency tolerance.
Cons: Expensive, more difficult to manufacture, sensitive to mechanical stress.
3. Polyimide
A flexible, heat-resistant material ideal for flexible PCBs and aerospace applications.
Pros: Excellent thermal resistance, flexibility.
Cons: Higher cost, more complex processing.
4. Metal Core PCBs (MCPCBs)
Feature an aluminum or copper core to enhance heat dissipation—perfect for LED and power electronics.
Pros: High thermal conductivity, structural durability.
Cons: Limited layer count, less flexibility in design.
5. Ceramic Substrates
Used in harsh environments like automotive and medical devices.
Pros: Exceptional thermal stability, electrical performance, and reliability.
Cons: Very high cost, fragile if not handled properly.
How Material Choice Affects Performance
1. Signal Integrity
In high-speed or high-frequency applications, material dielectric constant (Dk) and loss tangent (Df) are critical. Higher-end laminates like Rogers materials maintain signal integrity better than FR4, especially in microwave and RF systems.
2. Thermal Management
Devices that operate under high loads or constant usage—such as power converters or LEDs—benefit from materials with high thermal conductivity, like metal-core or ceramic boards.
3. Mechanical Reliability
In environments with frequent vibrations or temperature cycling (automotive, aerospace), materials like polyimide or ceramic provide greater longevity and stability.
4. Design Flexibility
Flexible PCBs demand materials that can bend without cracking. Polyimide and some PET materials meet this need, though they come with higher cost and complexity.
Cost Considerations: Balancing Performance and Budget
Choosing the “best” material doesn’t always mean selecting the most advanced one. It’s about cost-to-performance balance. For consumer electronics, FR4 may be sufficient and cost-effective. But for telecom infrastructure or defense systems, cutting corners with material can lead to significant performance failures.
Key cost drivers include:
Material procurement cost
Manufacturing complexity
Yield rate during production
Testing and validation time
Long-term reliability/maintenance cost
OEMs and startups alike must factor in not just upfront cost, but also total cost of ownership over the product lifecycle.
When to Consider Upgrading PCB Materials
You may want to move beyond FR4 when:
Your device operates above 1GHz
You’re experiencing heat-related component failures
You're entering rugged or high-reliability markets
You’re developing next-gen wireless, automotive, or medical devices
Working closely with your PCB manufacturer can help optimize material selection without blowing the budget.
Final Thoughts
Material selection is one of the most underestimated but vital decisions in PCB design and manufacturing. By understanding the properties, limitations, and ideal applications of different substrates, businesses can ensure their products not only perform well but also stay within budget.
Ultimately, the right material enables the right performance—for the right price.
コメント