The Growing Importance of PCBs in Medical Devices
- SUNSOAR TE.
- Mar 7
- 4 min read
Introduction
Medical devices have come a long way in the past few decades, evolving into highly advanced machines capable of monitoring, diagnosing, and treating a range of health conditions. Behind the success of these devices lies a critical component: printed circuit boards (PCBs). PCBs are not only essential for ensuring the functionality of medical equipment, but they also play a vital role in improving patient care. In this article, we will explore how PCBs are advancing the medical industry, the challenges of PCB design for medical devices, and what the future holds for this intersection of technology and healthcare.
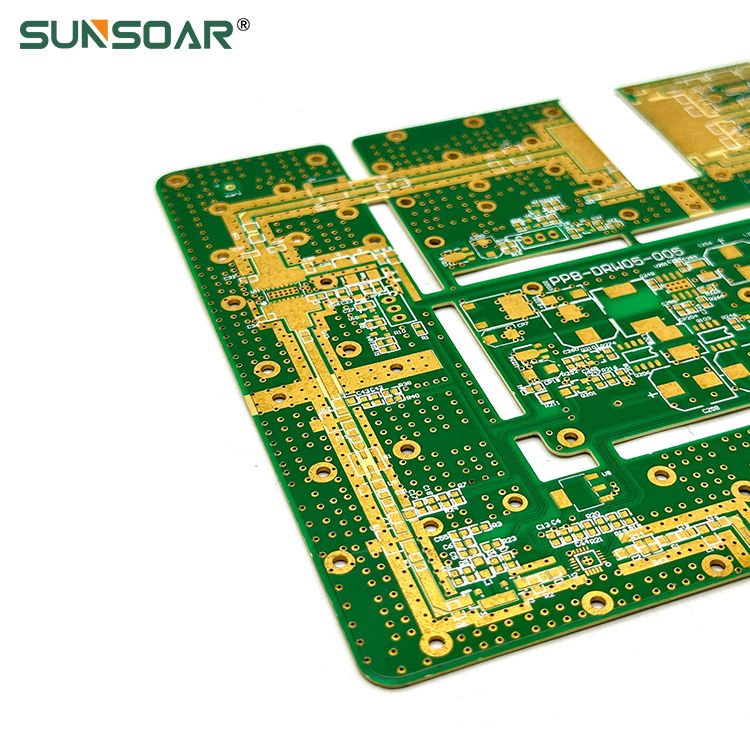
1. The Role of PCBs in Medical Devices
PCBs are the foundation of most medical electronic devices, connecting components and enabling them to communicate with one another. Whether it's a portable diagnostic tool or a life-saving surgical machine, PCBs ensure that electronic circuits are properly connected, making the device work as intended. Some key applications include:
1) Diagnostic Equipment
Function: Powers devices such as MRI machines, CT scanners, and electrocardiograms (ECGs).
PCB Type: Multilayer PCBs, flexible PCBs for sensor applications.
Impact: Provides accurate data acquisition, reliable imaging, and real-time monitoring of vital parameters.
Diagnostic equipment relies on complex PCB designs to process data from various sensors and imaging systems. These devices need to operate with extreme precision, and PCBs ensure that they deliver accurate, real-time results.
2) Wearable Health Devices
Function: Tracks health metrics like heart rate, blood pressure, blood glucose, and even electrocardiograms (ECG).
PCB Type: Flexible and thin PCBs, rigid-flex PCBs.
Impact: Allows for continuous monitoring and tracking of health data, enabling early detection of issues and personalized treatment.
With the rise of wearable devices for health monitoring, PCBs play a crucial role in miniaturizing electronics without sacrificing performance. These small, powerful PCBs enable devices like fitness trackers and smartwatches to deliver valuable health insights.
3) Implantable Medical Devices
Function: Powers devices like pacemakers, cochlear implants, and insulin pumps.
PCB Type: Biocompatible PCBs, flexible PCBs for in-body sensors.
Impact: Provides reliable power and communication, improving quality of life for patients with chronic conditions.
Implantable devices have unique challenges, including biocompatibility, miniaturization, and power efficiency. PCBs in these devices must meet stringent medical standards while being small and efficient enough to function inside the human body.
4) Surgical Instruments and Robotics
Function: Powers robotic surgery equipment, precision instruments, and other surgical devices.
PCB Type: High-precision PCBs, low-inductance PCBs for real-time control.
Impact: Enhances the accuracy and safety of surgeries by providing precise control over surgical robots and instruments.
Surgical robotics and precision instruments rely on PCBs to control motors, sensors, and actuators with extreme accuracy. This ensures that surgeries can be performed with the highest levels of precision, minimizing risks to patients.
2. Innovations in PCB Technology for Medical Devices
As the healthcare industry evolves, so too does the demand for more sophisticated medical devices. With advancements in PCB technology, new solutions are being created to meet the unique challenges posed by medical applications:
1) Miniaturization of PCBs
Why It Matters: Medical devices are becoming smaller and more portable, while still needing to offer high performance and accuracy.
Impact: Enables the development of smaller diagnostic tools, wearable devices, and implantable technologies without sacrificing functionality or power.
Miniaturized PCBs are particularly important in applications like wearable health devices and implantable devices, where space is limited but functionality is critical.
2) Biocompatible PCBs
Why It Matters: Implantable devices must be safe for long-term contact with human tissue.
Impact: Ensures that PCBs are safe for use inside the body, avoiding reactions that could cause harm or interfere with the device's functionality.
Biocompatible PCBs are crucial for devices like pacemakers and cochlear implants. These PCBs must meet strict medical standards to ensure they don't pose any risks to patients.
3) Flexible PCBs for Wearable and Implantable Devices
Why It Matters: Many medical devices need to be conformable to irregular shapes or embedded in wearable or implantable devices.
Impact: Offers greater design flexibility, allowing medical devices to be more comfortable and functional for patients.
Flexible PCBs are essential for wearable medical devices like fitness trackers and smartwatches, as well as implantable devices, which must conform to the contours of the human body.
4) High-Reliability PCBs
Why It Matters: Medical devices must operate flawlessly in critical situations, where failure could result in severe consequences.
Impact: Guarantees that the PCBs in medical devices are durable, dependable, and able to function under extreme conditions.
High-reliability PCBs are necessary for diagnostic equipment and life-saving devices like pacemakers, where any failure could have serious ramifications.
3. The Future of PCBs in Medical Devices
The future of medical devices will see continued advances in both medical technology and PCB manufacturing. Some of the key trends shaping the future include:
Telemedicine and Remote Monitoring: The rise of telemedicine will drive demand for remote monitoring devices, requiring efficient and reliable PCBs for constant connectivity and real-time data transmission.
Wearable and Implantable Health Devices: With more patients opting for continuous monitoring, PCBs will be critical in the development of wearable and implantable devices that are smaller, more powerful, and more comfortable.
AI Integration: Artificial intelligence will be integrated into medical devices to enable better decision-making and automation. This will require advanced PCBs capable of processing large amounts of data in real-time.
Sustainability in Medical Devices: The push for environmentally friendly products will lead to the development of eco-friendly, recyclable PCBs for medical devices.
Conclusion
PCBs are central to the functionality and advancement of medical devices, enabling critical innovations in diagnostics, treatment, and patient care. As the medical industry continues to evolve, the demand for smaller, more reliable, and high-performance PCBs will increase. Whether it’s for diagnostic equipment, wearable health devices, or implantable medical technologies, the role of PCBs will continue to expand, offering greater possibilities for improving healthcare outcomes.
Komentarze